콘크리트 부유구조체 적용을 위한 구조용 경량콘크리트의 최적배합비 선정
Determination of Structural Lightweight Concrete Mix Proportion for Floating Concrete Structures
Article information
Abstract
본 연구에서는 콘크리트 부유체 건설에 사용하기 위한 구조용 경량 콘크리트의 최적 배합비를 도출하기 위해 실험적 연구를 수행하였다. 경량콘크리트에 요구되는 설계압축강도 및 단위중량은 동적안정성 해석 및 기존에 건설된 부유식 구조물의 조사결과를 바탕으로 60 MPa, 1,800 kg/m3로 각각 설정하였으며 슬럼프를 측정하여 워커빌리티를 조사하였다. 실험을 위해 대표적 인공경량골재인 expanded slate, expanded clay, expanded shale을 사용하여 설계조건을 만족할 때까지 콘크리트를 반복 타설하여 최적 배합비를 도출하였다. 콘크리트의 배합에 대하여 NT Build 492, ASTM C 1202와 같은 염소이온 침투 저항성 실험을 실시하였으며 결과분석을 통해 경량콘크리트의 내구성에 미치는 실리카흄과 고로 슬래그 미분말의 영향을 조사하였다. 실험결과, 실리카흄을 시멘트대비 10%로 치환하고 expanded slate 또는 expanded clay를 사용하여 제작한 경량콘크리트가 모든 조건을 만족하였다. 마지막으로 구조용 경량골재의 선정, 경량콘크리트의 제작 및 시공시에 유의할 점에 대하여 설명하였다.
Trans Abstract
This study aims to provide information for the design and use of structural lightweight concrete (SLWC) for floating concrete structures in a marine environment. An experimental program was set up and comprehensive experimental campaign were carried out to determine SLWC mix proportions that can satisfy specified concrete strength, density, and slump values all of them were determined from previous research. Comparisons with previous SLWC mix designs that have been utilized for actual floating concrete structures were made. Key aspects needed to be considered regarding to the use of SLWC for floating marine concrete structures were discussed.
1. Introduction
Structural lightweight concrete (SLWC) has been widely utilized for various concrete structures including breakwaters, floating bridges, floating oil and gas storage tanks, and offshore structures. Compared to the conventional normal weight concrete (NWC), SLWC has many advantages such as reduced unit weight, better thermal insulation characteristics, and enhanced durability, all of which can contribute to a longer service life of floating concrete structures. Especially, reduced concrete density contributes to both the increase in buoyancy and reduced cross-sectional areas of structural elements. More space or span length are then available to make when applying SLWC in floating concrete structures such as platforms and bridges (Chia and Zhang, 2002). Fig. 1 shows offshore and floating concrete structures constructed with using SLWC (Sandvik et al., 2004).
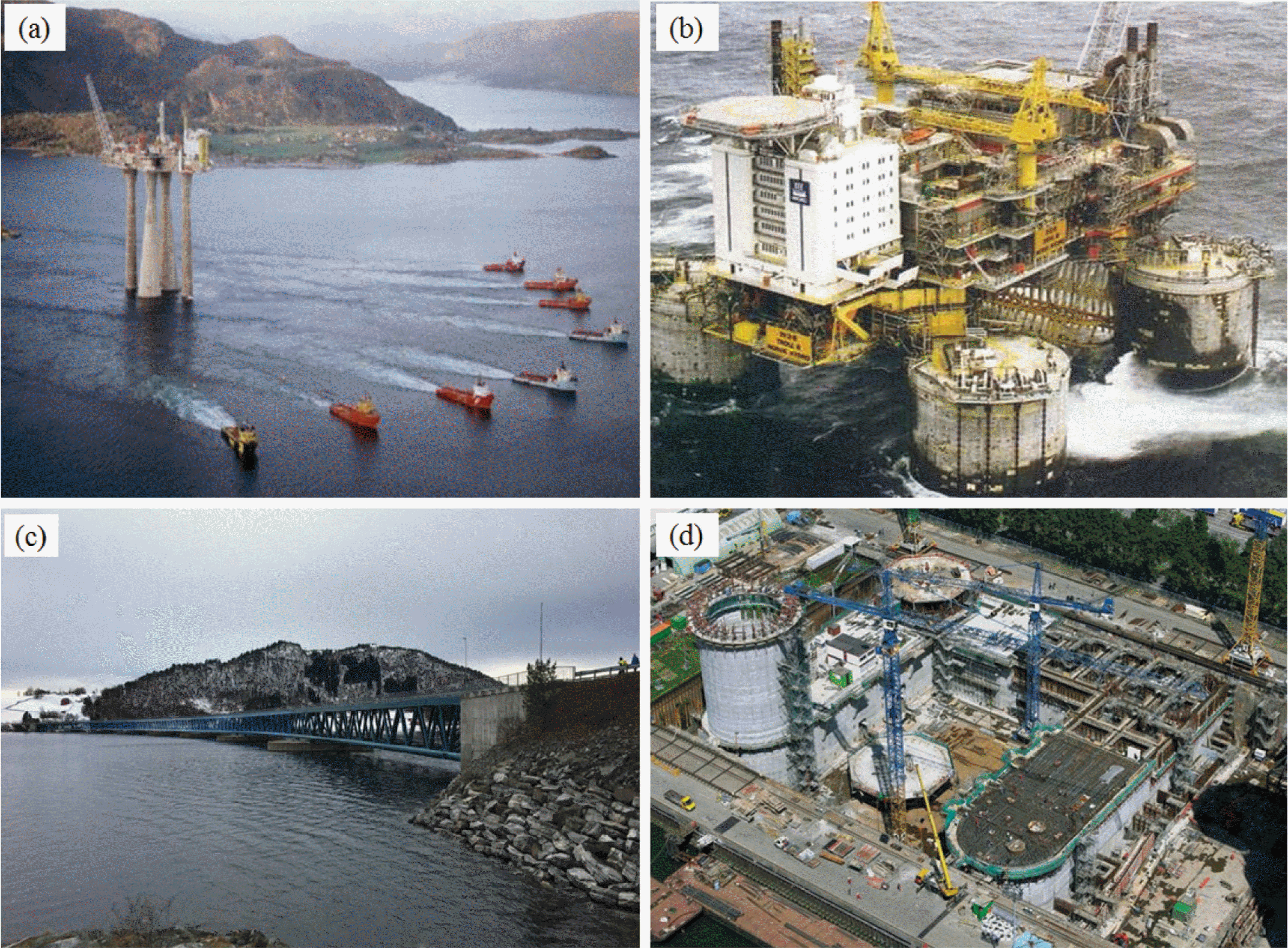
Offshore and Floating Concrete Structures Constructed with the Use of SLWC (a) Troll A Platform (Sandvik et al., 2004); (b) Troll B Platform; (c) Bergsøysund Bridge; (d) Multi-Purpose Unit Heavy Lifter.
Both concrete strength and density are two important considerations for structural designers or engineers who consider using SLWC for floating concrete structures. Previous research concluded that the reduced concrete density(lower than 1,800 kg/m3) greatly contributed to the better stability of a floating oil storage tank subjected to wind and current loads as illustrated in Fig. 2 (Jiang et al., 2017).
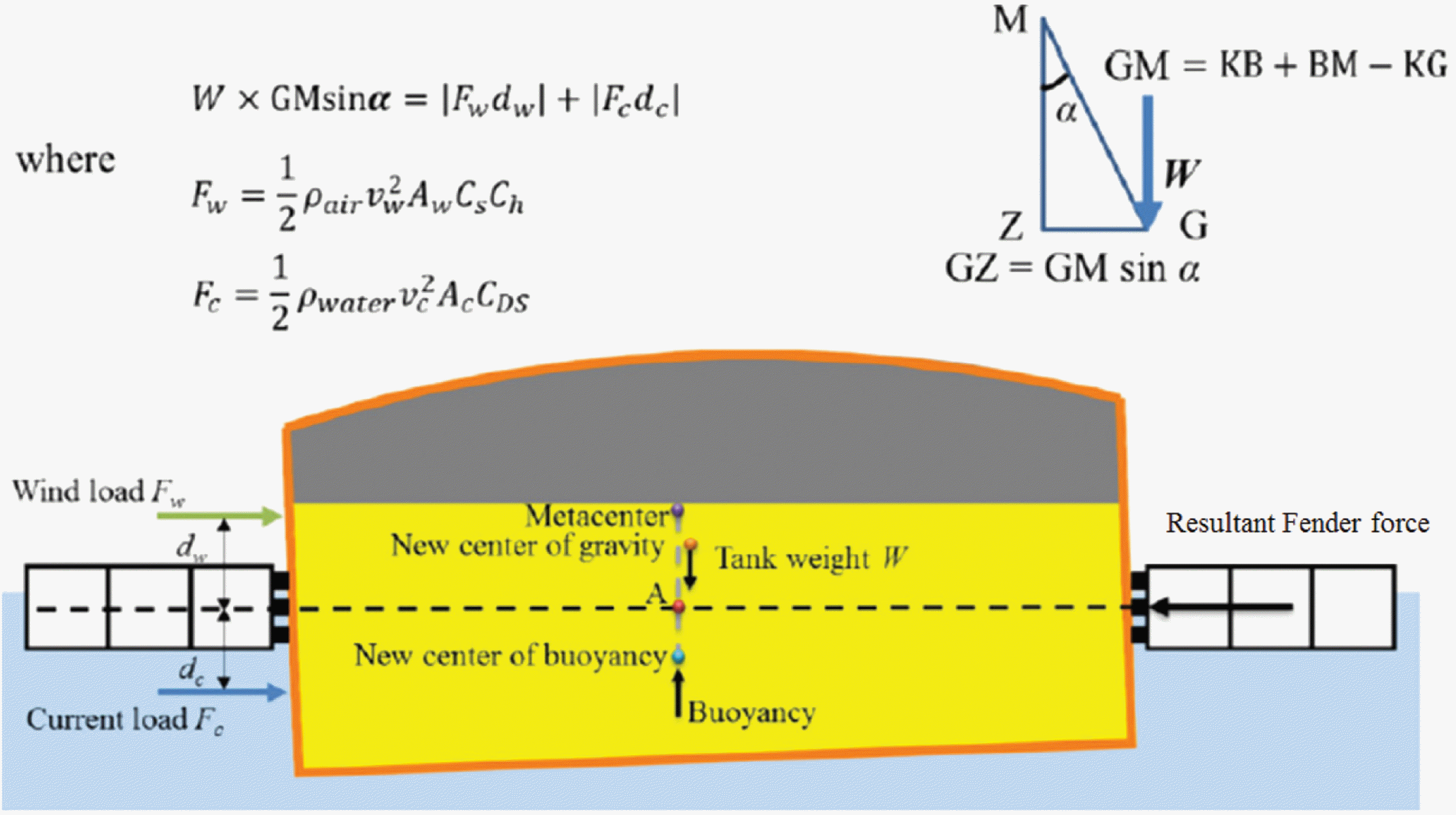
Stability Analysis of Floating Oil Storage Tank (Jiang et al., 2017).
High strength SLWC can easily be produced using suitable type of aggregates and concrete recipes. In the SLWC, the lightweight aggregate (LWA) is the weakest component due to its lower strength and stiffness compared to the paste and interfacial transition zone. Namely, SLWC has weaker bond between the coarse and mortar compared to that of NWC, and crack initiation and propagation processes might be different when they subjected to compression as shown in Fig.3 (FIP Manual of Lightweight Aggregate Concrete, 1983).
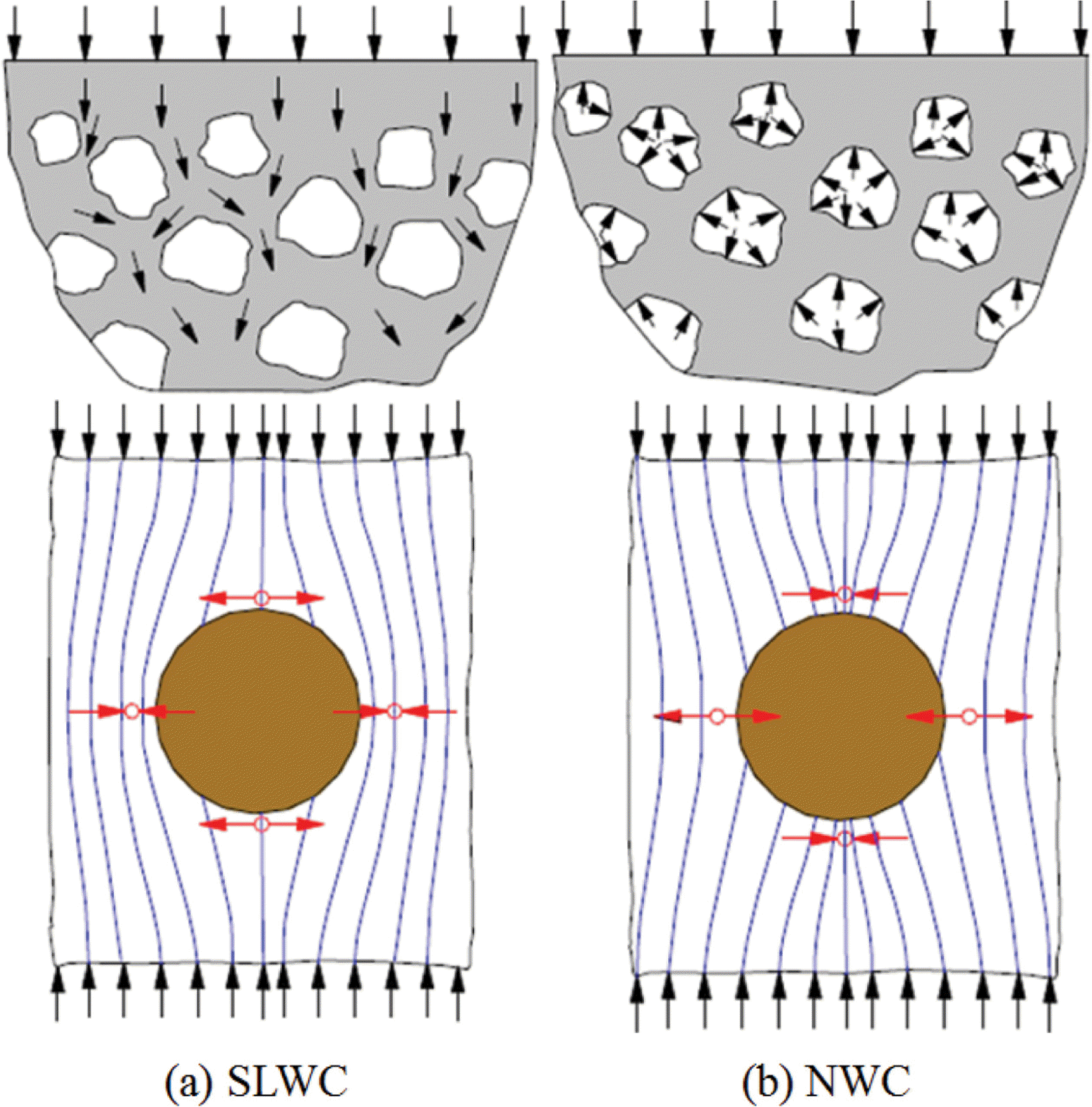
Force Transfer Difference between SLWC and NWC under Compression (FIP Manual of LWC, 1983).
Many researchers have pointed out that the type of LWA selected plays a significant role in the physical, mechanical, and thermal properties of SLWC produced (Rossignolo and Agnesini, 2002; Demirboga and Gul, 2003; Chi et al., 2003; Lo et al., 2007; Kim et al., 2010). Compared to normal weight aggregate (NWA), LWA has a higher internal porosity, and that is the primary reason for the low apparent specific gravity of the aggregate. LWA’s high water absorption is an important concern for structural applications. For instance, the loss of workability can be a serious problem if LWAs continuously absorb water during the concrete production, and the amount of absorbed water has a considerable influence on the density of the concrete leading to reduced buoyancy of floating structures. Table 1 summarized the previously constructed offshore and floating concrete structures with the use of SLWC. The product name of LWAs applied for each structure were also included in the table. The most common types of LWAs that has been frequently utilized in floating concrete structures were expanded clay and expanded slate.
Marine concrete structures are directly exposed to a harsh environment that can accelerate concrete deterioration and reduce the service life of structures. Concrete deterioration in the marine environment is much more complicated since the synergistic effects are common between different constituents/mechanisms. Most of the concrete deterioration in marine environments is caused by constituents in seawater that contains 3.5% (35 g/L) of dissolved salt and principleions are Na+, Mg2+, Cl−, and (SO4)2− (Metha, 1991). In addition to dissolved salt, certain gases around a structure play a role in chemical or electrochemical reactions that can influence the concrete durability. Seawater temperature is also an important consideration for concrete durability, since high variations in temperature can increase the rate of chemical or electrochemical reactions in floating reinforced concrete structures. It should be noted that there is a marked difference between sea-surface and atmosphere temperatures. Rather than other constituents in seawater, chloride ingression is the main cause of steel corrosion in the marine environment and corrosion initiation has been taken as failure criteria for durability analyses and servicelife predictions for marine concrete structures (Ferreira, 2009). Both concrete quality and exposure conditions are two key parameters in determining the rate of chloride ingress based on the measured diffusion coefficients and surface chloride concentration (Costa and Appleton, 1999). This is because concrete pore structure is influenced by the quality of concrete, and the harsh marine environment might increase the water content in the pore structure, which affects the ingression of chloride.
Improved concrete durability through the use of SLWC was reported based on field measurements conducted on existing breakwater structures (Sturm et al., 1999). However, not all types of LWAs can be utilized for such floating concrete structures because SLWC properties can be variable depend on the aggregate type selected, aggregate presoaking condition, concrete mixing and casting procedures. A great number of experimental studies have been carried out to investigate the effects of LWA types and/or supplementary cementitious materials (SCMs) on concrete mixing, chemical and physical properties, and durability of SLWC. The initial water curing during the first few days after concrete mixing have a significant influence in increasing the strength and enhancing the durability of the SLWC under hot marine exposure conditions (Haque and Al-Khaiat, 1999; Haque et al., 2004; Haque et al., 2007). SLWC with SCMs such as silica fume and fly ash exhibited the higher material strength, lower chloride-ion ingress, and improved resistance against sulfate attack (Babu and Babu, 2003; Tanyildizi and Coskun, 2008).
As summarized previously, many experimental studies have been conducted to clarify the effects of SCMs on the physical property and durability of SLWCs. However, the use of SLWC for floating concrete structures in a marine environment has not been well explored yet. This might due to the relatively more conservative nature of the marine and offshore industry, the less wide spread in using concrete as a structural material for such construction, and lack of well-developed design guides to determine of SLWC mix proportion. In this regards, the main objective of this paper is to provide information for the design and use of SLWC for floating concrete structure in a marine environment. To this end, an experimental program was set up and comprehensive experimental campaign were carried out to determine SLWC mix proportions that can satisfy specified concrete strength, density, and slump. Comparisons with previous SLWC mix designs that have been utilized for actual floating concrete structures were made. Lastly, key aspects needed to be considered regarding to the use of SLWC for floating marine concrete structures were discussed.
2. Experimental Investigation
2.1 Concrete Mix Design Requirements
Based on the literature review about existing floating concrete structures, it can be seen that designed concrete strength ranges between 42 and 80 MPa while density ranges between 1,600 and 2,250 kg/m3(See Table 1). Previous research concluded that the effect of concrete density on the stability of floating oil storage tank subjected to wind and current loads is much more significant compared to that of strength. More details regarding the relationship between the concrete density and stability can be found out from previous research (Jiang et al., 2017). Thus, mix design requirements in this study were specified as 28 days compressive strength of 60 MPa and 1 day concrete density of 1,800 kg/m3.
2.2 Materials
As shown in Fig. 4, total three different types of lightweight coarse aggregates (CAs) and three different types of lightweight fine aggregates (FAs) were considered as test variables in this study. NWC with Natural CA was also prepared for the comparison purpose. Expanded slate CA, named ‘Stalite’, has the particle density of 1,394 kg/m3 and 24h water absorption ratio of 5.9% while expanded clay CA, named ‘Liapor 4/8’, has the particle density of 1,449kg/m3 and water absorption ratio of 11.9%. Expanded shale aggregate, named ‘Asanolight’, has the particle density of 1,277 kg/m3 as well as the water absorption ratio of 11.2%. Stalite and Liapor 4/8 are two most common CAs been applied for floating concrete structures as mentioned previously.
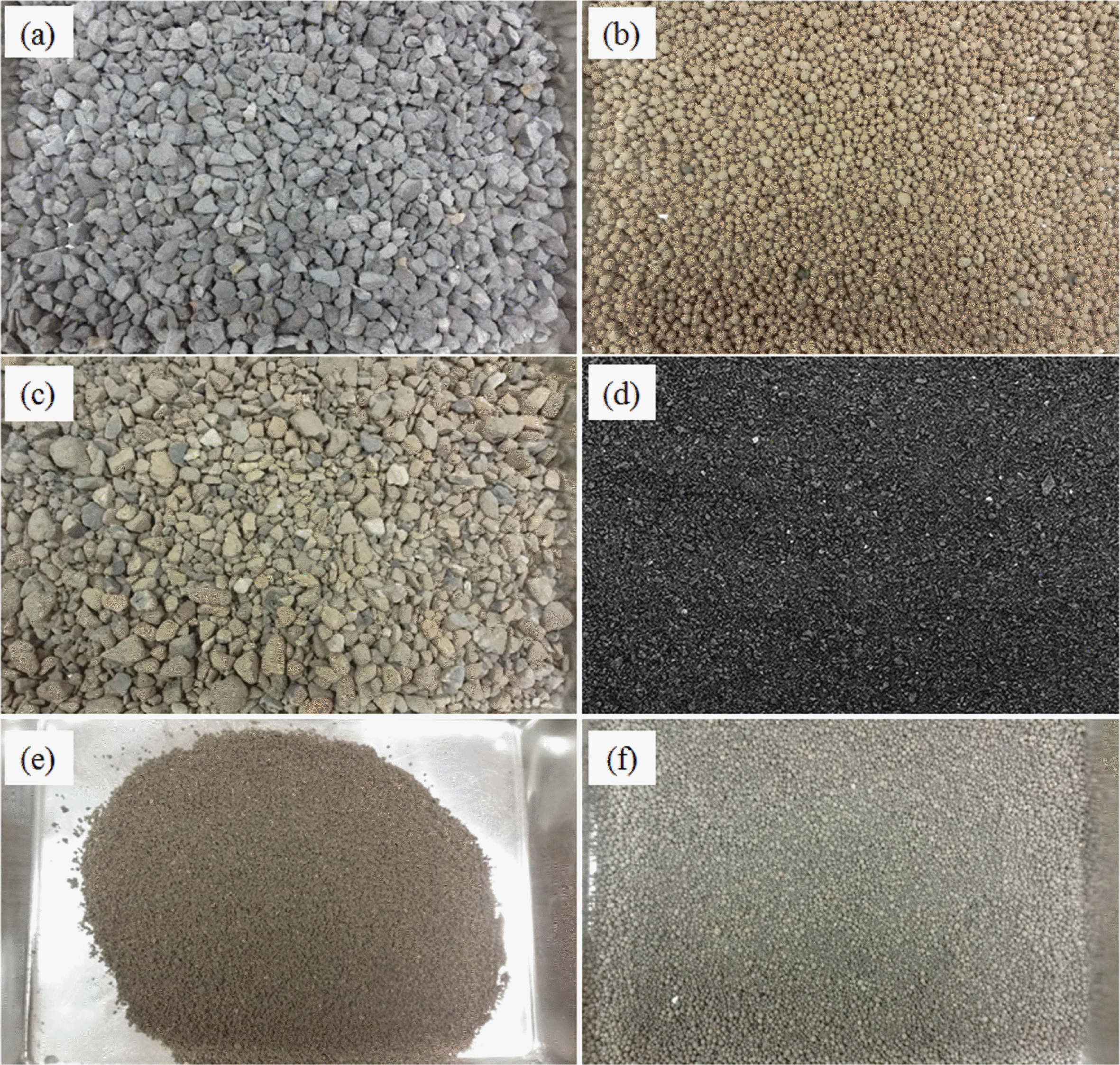
Investigated Lightweight Aggregates (a) Stalite Coarse; (b) Liapor Coarse; (c) Asanolight Coarse; (d) Stalite Fine; (e) Asanolight Fine; (f) Liapor Fine.
In addition to different aggregate type, the effects of silica fume (SF) and ground-granulated blast-furnace slag(GGBS) on the strength development and durability of SLWCs were considered as test variables. Type I ordinary portland cement with a specific density of 3.14 g/cm3, SF containing about 92% of SiO2 with a density of 2.27 g/cm3, GGBS containing 32% of SiO2 and 38% of CaO with a density of 2.94 g/cm3, and blaine surface area of 4,070 cm2/g were used. The high range water-reducing super-plasticizer of polycarboxylate was applied at constant rate of 1.0% of the binder content weight. The size distribution of aggregates were investigated as shown in Fig. 5.
2.3 Aggregate Preparation and Mixing Procedures
All lightweight CAs were pre-soaked for 24 hours prior to the concrete mixing to reduce aggregate water absorption during the mixing and casting. Surface water of presoaked aggregates was then removed with using dried towels to make a surface-saturated dry (SSD) condition. Repeated concrete mixing, concrete slump and density measurements were carried out until all measured values satisfy the design requirements. Table 2 shows the SLWC mix proportions investigated in this study.
Each mixture was labeled as ‘ST’, ‘LI’, and ‘AS’ according to the product name of CAs. Cement was partially replaced with SF of 0%, 10%, and 20% and GGBS of 0%, 25%, and 50%.
Followings are detailed mixing procedures adopted in this study. Total concrete mixing time was 5 minutes.
(1) All CAs were pre-soaked for about 24 hours prior to start mixing
(2) CAs were then surface dried with absorbent cottontowels
(3) Three lightweight FAs (Asanolight, Liapor, and Stalite), natural CA and FA were prepared as no pre-soaked condition
(4) All materials were then placed into a drum type pan mixer
(5) Concrete mixing was carried out for one minute with half of total water
(6) After one minute of mixing, remaining water were added and mixing continuously conducted for additional 4minutes.
2.4 Tests and Measurements
Compressive strength was measured according to BS EN 12390-3 using three 100 mm cubical specimens at 1, 7, and 28 days. Fresh and 1 day demolding density of SLWCs were determined according to ASTM C138 and BS EN 12390-7, respectively. Oven dried density was recorded according to BS EN 206-1. Chloride penetration resistance was evaluated using 100 mm diameter and 50 mm length discs cut from 100 mm diameter and 200 mm length cylinders after the top and bottom portions removed. Two different types of tests were implemented in this study to investigate the chloride penetration resistance of SLWCs. As shown in Fig. 6, the first one is rapid chloride penetration test (RCPT) in compliance with ASTM C1202 and the other one is rapid migration test according to NT Build 492 that can estimate the chloride diffusion coefficient based on the measured chloride penetration depth.
3. Results and Discussions
3.1 Effects of Aggregate Type on Strength and Density
In general, coarse and fine aggregates play a significant role in strength, since it makes up about 60~70% of the total volume of the concrete mix. Table 3 summarized measured compressive strength, density, and slump values for all mixtures investigated in this study. Strength and density values were averaged from three separated measurements. Stalite-based SLWC showed the higher strength than Liapor-based and Asanolight-based SLWCs, as expected. This might be related to the particle density of aggregate as many researchers pointed out. Aggregate strength is also one of the most important factors determining the concrete strength while this was not included in the range of this study. Aggregate type did not show significant influences on the measured concrete density. All lightweight concrete(ALWAC) showed the improved workability while the strength was reduced.
3.2 Effects of SCMs on Strength Development and Concrete Durability
The addition of silica fume (SF) does not influence much the early strength gain between 1 and 7 days as shown in Fig. 7. However, the effect of SF on the compressive strength at 28 days was clearly confirmed. Specifically, the strength increased by 7 to 13% compared to that of plain concrete. The effect of ground-granulated blast-furnace slag(GGBS) on the compressive strength measured between 1 and 28 days was not significant regardless of its replacement ratio.
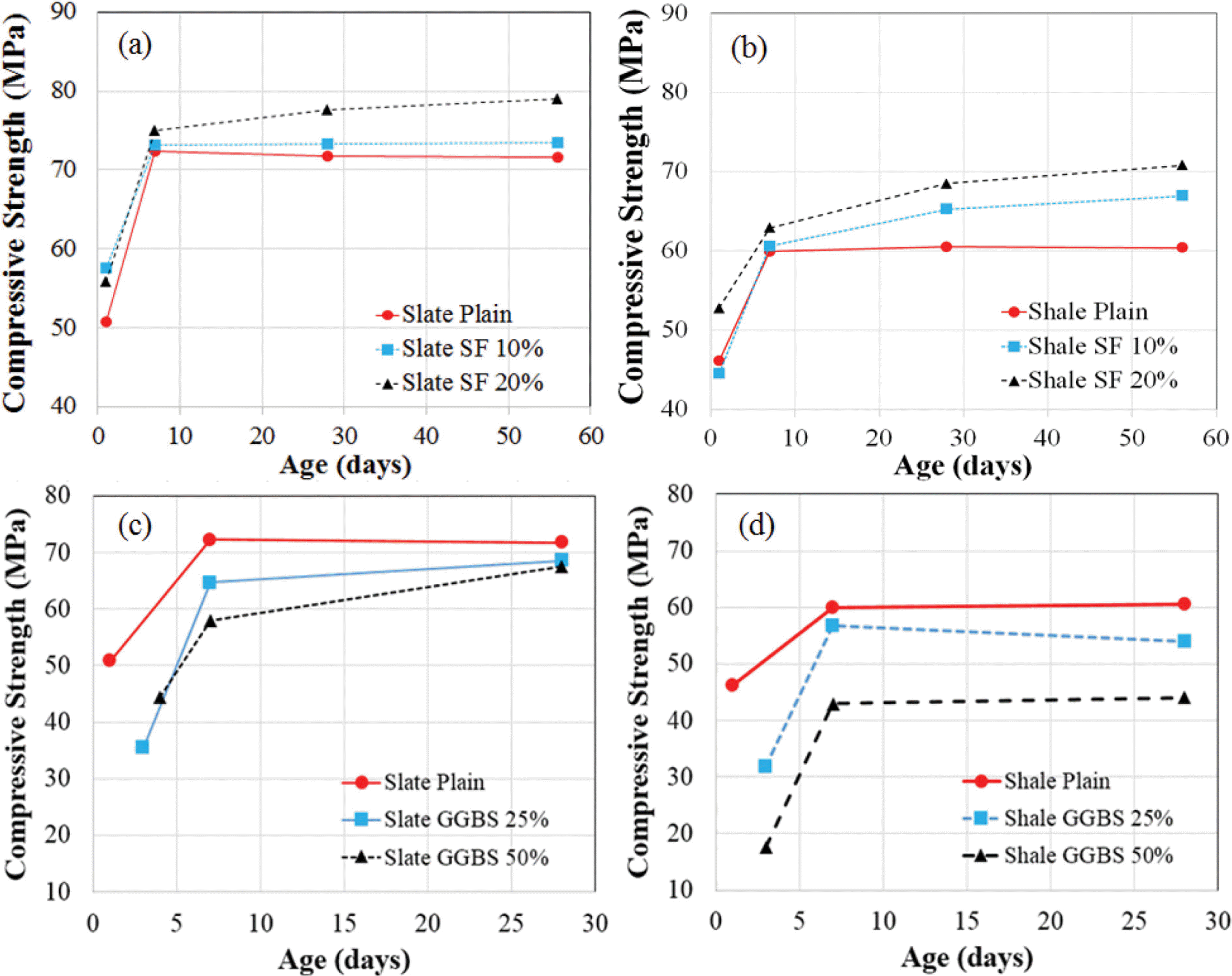
Effect of SCMs on the strength development (a) and (c): Stalite-based SLWC; (b) and (d): Asanolight-based SLWC.
Importantly, 1 day strength of SLWC containing GGBS was significantly lower than that of plain concrete. This low early strength gain with GGBS may be due to slow hydration process with higher amount of slag content. However, long-term strength development can be expected if moisture remains available for further reactions between primary hydration product Ca(OH)2 and GGBS as Li and Yao, 2001 and Choo and Newman, 2003 pointed out. Silica fume addition rates did not show any significant influences on the concrete slumps. This might be due to low addition rate of SF investigated. Fig. 8 shows the some representative SLWC slumps measured in this study.
Especially in SLWC, oven-dry density is an important consideration since it can directly influence the strength. Fresh density of SLWCs were gradually decreased according to the increase of SF while GGBS showed no effects on measured densities. The mean weight differences between fresh and oven-dry densities in SLWC with Stalite and Asanolight were 134.4 kg/m3 and 269 kg/m3, respectively. The mean weight differences to the fresh density ratio for SLWC with Stalite and Asanolight were 8.1% and 17.0%, respectively.
Two different rapid chloride-ion penetration tests were conducted to evaluate the difference among types of CAs, SF replacement level. The effect of GGBS replacement on the resistance to chloride penetration was not investigated at this time since this study focuses more on the early-age properties. The total charge passed and chloride diffusion coefficient were both decreased with the increase of SF content. Stalite-based SLWC showed the higher resistance against chloride penetration compared to that of Asanolight-based SLWC. Calcium hydroxide in hydrated cement is converted to calcium silicate hydrates by reacting with silicates in SF. Thus, it is considered that the resistance to chloride penetration of concrete was affected by not only the type of CA but also the microstructure of hydrated cement. All mixtures exhibited quite similar values of diffusion coefficient when SF was added. This might due to the enhancement of pore distribution and microstructure by using SF as Youm et al., 2016 pointed out.
3.3 Lightweight Concrete Mix Proportions Satisfying Specified Design Requirements
Two best mix designs that satisfy design requirements for targeted floating concrete structures were ST SF-10-1 and LI SF-10-1 as shown in Table 2. Both mixtures also exhibited the good workability and consistency compared to other mixtures. Note that Stalite aggregate can be utilized for concrete pumping due to the relatively low water absorption under the high water pressure compared to expanded clay aggregates such as Liapor and Leca 800. Lower concrete density can be achieved when using both lightweight CA and FA. For example, ALWC with both Stalite fine and coarse aggregates exhibited better workability without any bleeding issues. Some studies concluded that proper use of natural aggregates in SLWC can contribute to make a good concrete. However, extensive trial mixing might be necessary to ensure the quality of concrete.
Based on experimental results, two mix proportions (ST-SF-10-1 and LI SF-10-1) both can satisfy design requirements were introduced in this study. All other proportions except for two mix proportions (namely, ST-SF-10-1 and LI-SF-10-1) did not satisfy the requirements. It should be noted that there are no mature guidelines to determine the mixture design of SLWC based on the LWA type, concrete strength, and density requirements. Thus, preliminary test or trial mixtures are necessary to determine the optimum mix design of SLWC for targeted floating concrete structures.
Table 4 shows the summary of SLWC mix designs that were applied for existing floating concrete structures. It can be seen that applying natural aggregates in SLWC might increase both the strength and density. It should be noted that reducing concrete density is much more tricky compared to the increase of strength and the relationship between strength and density is not always proportional. This all caused by high water absorption rate of LWAs.
Recently, two SLWC mix designs were reported by Justnes et al., 2016. According to the first design below, compressive strength higher than 60 MPa and demolding density of 1,850 kg/m3 can be produced with using expanded clay aggregates such as Leca 800 or any LWAs with equivalent bulk density.
650 kg binder
685 kg NWA (e.g. granite) (0-8 mm)
260 kg LWA (4-8 mm)
260 kg LWA (0-12 mm)
This design includes NWA, thus, it might be more cost effective compared to ALWAC.
Very low demolding density such as 1,450 kg/m3 can be also produced with the second design introduced below, but the strength will be decreased compared to the first one.
660 kg binder
140 kg LWA (0-3 mm)
85 kg LWA (1-4 mm)
240 kg LWA (4-8 mm)
240 kg LWA (8-12 mm)
Two suggested mix designs can be adjusted according the use of SCMs, the type of super-plasticizer, and absorbed water content of LWA to satisfy design requirements.
3.4 Discussions and Recommendations
Mix design of SLWC has to be given more attention than that of NWC since more parameters such as low aggregate density and high water absorption need to be considered. For the same reason, the absolute volume method to measure air content cannot be used for SLWC without extra caution. There are no mature guidelines to determine the mixture design of SLWC based on the LWA type, concrete strength, and density requirements. Some researchers proposed detailed aggregate preparations and mixing procedures based on the test results with limited number of specimens. Most of them are valid only for laboratory testing not for real-scale concrete mixing. Thus, preliminary test or trial mixtures are necessary to determine the optimum mix design of SLWC for targeted floating concrete structures. It is not recommended to directly batch and mix with dried LWAs, because the aggregate particles continuously absorb the water from the mix. For instance, the loss of workability can be a big problem if LWAs continuously absorb water during the concrete production, and the amount of absorbed water has a considerable influence on the density of the concrete leading to reduced buoyance of floating structures. In this regards, the use of pre-soaked LWA is recommended to ensure a robust concrete recipe.
The physical and mechanical properties of SLWC are mainly determined by the type of aggregate, particle density, and aggregate water absorption. SLWC with high compressive strength can easily be produced with a suitable concrete mix design and LWA. It cannot be simply concluded that which type of structural LWA is mostly preferred for floating concrete structures. However, it is reasonable to focus on selecting LWA can contribute the high strength/density ratio of SLWC and low water absorption. Extensive mix tests is important to determining the suitable type of LWA since water absorption rate can be variable depends on the environmental conditions such as humidity and temperature.
In general, SLWC exhibits better durability performance compared to that of NWC under the same exposure conditions. This might be due to the high quality of the interfacial zone between the paste and aggregate as well as the better elastic compatibility of the aggregate with the surrounding mortar. The durability performance of floating concrete structures in harsh marine environments depends on many factors such as chlorides, sulfates, temperatures, tidal action including repeated wetting and drying, high hydrostatic pressures, and the growth of marine organisms. In this regards, long-term durability experiments that can consider chemical or electrochemical reactions between concrete and seater must be accompanied. Carbonation, alkali-aggregate reaction, and sulfate attack can be prevented with the addition of SCMs such as silica fume, fly ash, and calcined clay. Surface coating such as epoxy coating or cathodic protection can be utilized in order to prevent chloride ingress into the concrete and rebar corrosion initiation, respectively, and extend the service life of floating concrete structures.
4. Conclusions
The tests performed in this research project are aimed to investigate whether the type of the aggregate, as well as selected supplementary cementitious materials may affect the strength, density, and durability of structural lightweight concrete. The focus of the experimental campaign is to determine the concrete mix proportion that can satisfy design requirements for the actual construction of floating concrete structures. Concrete mix designs were determined based on repeated concrete mixing and measurements.
The present study indicates that the type of lightweight coarse aggregate has a strong influence on the measured compressive strength. It was found that an increase in the particle density of lightweight corse aggregate increases the compressive strength of concrete. Overall, Stalite-based SLWC showed the best performance in compressive strength, density, workability, and consistency. The effects of silica fume on the compressive strength at 28 days and the resistance to chloride-ion penetration were obvious. In more detail, the compressive strength increased by about 10% and the chloride diffusion coefficient decreased by about 70%, respectively, compared to the plain concrete specimen. However, the study indicated that the addition of silica fume or ground-granulated blast-furnace slag had negligible effects on the early strength gain between 1 and 7days. Further studies may be necessary to identify the optimum replacement ratio of supplementary cementitious materials to increase the strength and improve the durability performance. The present results were obtained by compressive strength, density, and rapid chloride-ion penetration tests. Good understanding of concrete long-term behavior is basically important for floating concrete structures that constructed in marine environments. In this regards, further studies must be carried out to understand a long-term behavior such as strength development and durability of SLWCs produced with mix proportions introduced in this study. Fracture surface analysis must be conducted because crack initiation and propagation process of SLWC can be significantly different compared to that of NWC due to weaker bond between the aggregate and cement paste.
Based on both an experimental study and collected previous mix proportions, some important recommendations were made for better use of structural lightweight concrete for floating concrete structures. It was not able to conclude the best type of aggregate at this time because the best one can be different depend on the importability of lightweight aggregate, portion of concrete, type and location of targeted floating structure, and also environmental conditions. Pre-soaking of lightweight coarse aggregate, repeated concrete mixing, and measurements all must be carried out to determine a robust concrete recipe for floating concrete structures.
Acknowledgements
This work was supported by the “Development of Wave Power System for the Floating Light Beacon(Project Number: 20170323)”, and “Study of the tidal-current power generating system using concrete shroud (Project Number 20170122)”.